Isopig® - The Isolation Without Stress
- By Pipeline Pressure Isolation Group
- •
- 12 Oct, 2018
- •
IsoPig® - The Future of Pipeline Isolation
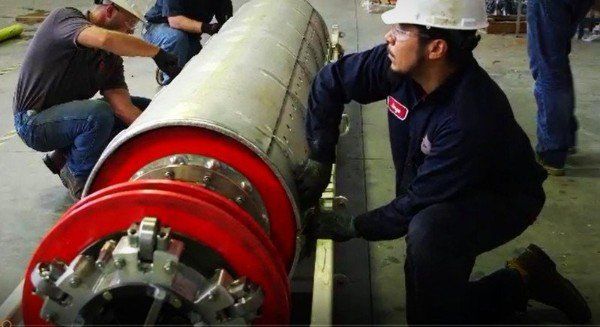
IsoPig® - The Future of Pipeline Isolation
Pipeline Pressure Isolation Group is a technologically advanced service company, formed to provide isolation/barrier service to oil & gas pipeline operators. PPIG’s IsoPig® is the world’s first piggable, low-stress pressure isolation plug, which can operate in thin wall onshore pipelines, as well as offshore pipelines.
The IsoPig® creates an energized, double-block, bubble-tight seal, for a hydrocarbon-free worksite. Isolation without stress on the pipe and operation:
· Minimal excavation work at location
· Reduced heavy equipment on site
· Traditional hot tapping procedures not required
· The need to purge or flatten the line is removed
· Pipeline left in superior condition, with the IsoPig® large holes are not cut into pipe
PPIG’s journey began with development of the 24” diameter IsoPig® tool. With a wide variety of pipeline sizes installed throughout the market, the offering expanded with designs for a tool with a 16” and 20” diameter. Table 1 highlights key operating features of each tool size within PPIG’s fleet.
Tool Diameter (in) |
Pressure Differential (psi) |
Bend Capability (D) |
24 |
1000 |
3 |
20 |
2220 |
1.5 |
16 |
2220 |
1.5 |
PPIG developed the IsoPig® (Figure 1) to allow isolation services where intervention and excavation create unnecessary burden. In short, the IsoPig® is a piggable tool that is stopped by flow and set to form a pressure barrier inside the pipeline.
The IsoPig® train consists of both a leading and trailing Control Module, with two adjacent Plug Modules at the center of the tool.
A transceiver communicates wirelessly with
the tool through the ground and then subsequently through the pipe wall,
instructing the tool to “set/unset”. Two
IsoPig® work in sequence to isolate the area of interest/worksite. Think of it
as a temporary blind flange, pigged to a worksite, so that work can be
performed while the pipeline remains pressurized. Once the work is finished each tool is unset
and pigged out of the line, or onto the next worksite.
The Control Module
The Control Module serves as the communications device, contains the actuation equipment for the Plug Module, and houses the battery power and antenna.
Each Control Module (Figure 2) actuates a plug module independently. The linkage between the plug modules is solely a mechanical linkage. There is no communication either electronic or hydraulic conduits between the plugs, creating a true independent, fully redundant tool.
Each Control Module houses logic to communicate through Extremely Low Frequency (~ 22 Hz) radio waves, which is transmitted and received through a transceiver. Multiple password access from a remote laptop in the field is required to set/unset the IsoPig®, with lock-out/tag-out features, and failsafe defaults to maintain the isolation.
This transceiver additionally is programmed to emit a pinging signal, allowing multi frequency tracking capability using a tracking device. This allows the operator to know the tools position as it moves along the pipeline and helps provides accurate placement.
The control module uses a lithium primary battery pack rated for twenty sets and twenty unsets. More than enough setting capacity for any normal operational sequence.
The Plug Module
The Plug Module maintains the plug position and creates the isolation. This is achieved through two simultaneous component setting actions, using grips and a packer (Figure 3). This actuation utilizes hydraulic fluid power from the Control Module and is maintained by multiple valves for redundancy.
The grips radially engage into the pipe wall to maintain plug position, through a wedging action. The differential pipeline pressure forces are radially transferred into the pipe wall. The grip plates are designed for maximum length, distributing this radial load over a large area. This key design feature is one reason the IsoPig® design induces low stress on the pipe wall during an isolation.
The packer is a rubber ring that is squeezed during activation to create the seal against the pipe wall, creating a “bubble-tight” isolation.
Once the hydraulic setting force obtains
initial sealing, additional pressure applied is proportional to the pressure
change across the tool. So, once set, a higher
pipeline pressure against the tool further strengthens the isolation (i.e.,
transfers longitudinal pressure circumferentially), which intensifies the tool
setting. The more differential pressure,
the greater the seal.
By dividing load paths internally in the Plug Module, only a percentage of the differential pressure end load is transferred through the packer. This feature reduces overall pipe stress induced by the packer, Isolation Without Stress.
Intrinsic seal extrusion mitigation features mean that the IsoPig® tooling does not require special adapter kits to be manufactured and outfitted. Therefore, IsoPig® trains are ready to be deployed and used in a wide range of pipe grades and wall thicknesses using standard configurations. The tool can be mobilized and, on the jobsite, much faster than conventional plugs.
Block and Monitor
The IsoPig® is a “block and monitor” tool, where pipeline pressure and temperature sensing is obtained through multiple monitor points in the train. Each Plug Module houses two pipeline transducers, one before and one aft of the isolation. This allows redundant monitoring of the high pressure, annulus pressure between each plug isolation, and low pressure behind the trailing module (Figure 4). Each Control Module additionally houses one pipeline pressure sensing transducer before and aft of the isolation for added redundancy.
The transceivers allow communication,
data transfer, and alarms to be directly sent to the end user/operator. Annulus
pressure criteria is defined, and thresholds are placed around allowable
acceptance criterion. With continuous
monitoring features, the on-site technician would be immediately notified of
any changes in the integrity of the isolation.
Applications
The IsoPig® can readily be used on a variety of applications associated with pipeline repair and maintenance:
· Midline Repairs
· Valve Repairs/Replacements
· Launcher/Receiver Repairs/Replacements
· Laterals/Proper Barred T’s
· Excavation Safety
· Hydrotesting
In addition, many regions in the United States have passed regulatory legislation that either prohibits, or strongly disapproves of venting gas due to green-house gas effects of methane emissions.
Also, many pipeline operators have their own internal goals and objectives related to emission mitigation. The IsoPig® is a leading solution for such environmentally friendly isolation applications, limiting emissions to the atmosphere, which could help operators meet these goals.
Conclusion
The IsoPig® is creating a paradigm shift in pipeline isolation where a much more efficient and cost-effective solution can be achieved.
And although pipelines are the safest form of transportation in comparison to other transportation methods[1], all eyes are upon the industry with zero incident expectations. Use of the IsoPig® provides an alternative method that will provide:
Less heavy equipment/heavy lifting on site.
Less personnel required working in the ditch.
Lower emissions using an environmentally friendly solution.
With the IsoPig®, pipeline isolation can be performed leaving the pipe in a far superior condition than with existing outdated methods. It is time for the industry to move forward and harness this innovative shift in pipeline isolation with the IsoPig®
Isolation Without Stress.
[1] Paul W. Parfomak, Keeping America’s Pipelines Safe and Secure: Key Issues for Congress (Congressional Research Service, 2013)